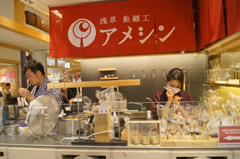
Thanks to, and photos courtesy of: Ameshin
Ameshin Website:</br >http://www.ame-shin.com/en/
■Tokyo Skytree Town Solamachi Store
For amezaiku demonstrations and sales
Block 11, East Yard, 4F, TOKYO Solamachi, TOKYO SKYTREE TOWN,
1-1-2 Oshiage, Sumida-ku, Tokyo, 131-0045
Nearest train stations:
Tokyo Skytree Station on the Tobu Line
Oshiage Station on the Toei Asakusa Line, the Keisei Oshiage Line,
and the Tokyo Metro Hanzomon Line
■Head Office in Asakusa
For amezaiku hands-on workshops
1F, 1-4-3 Imado, Taito-ku, Tokyo, 111-0024
A 10- to 15-minute walk from Asakusa Station on the Tokyo Metro Ginza Line, the Toei Asakusa Line, and the Tobu Line